Standard Plastics for Injection Molding Applications Injection molding is a process we use at our…
While we often discuss how medical injection molding and thermoforming allow for greater innovation and lower costs, we haven’t spent much time looking specifically at thermoplastics in dentistry. From improving safety and sterility to providing a more comfortable experience, it can be argued that plastics are doing just as much for dentistry as they are for the rest of the medical industry, and we wanted to take the opportunity to provide a closer look.
Improving Safety with Single-Use Items
For decades, most instruments and items used in dentistry were made from metal and designed to be used repeatedly. In between patients, instruments were disinfected and sterilized either in an autoclave that uses pressurized steam or with chemical vapor. Regardless of the method, it was a lengthy process that added more work on the dental team and required a continued rotation of equipment.
Today, many of the instruments dental professionals use are single-use, arriving in sterile packages and ready for patient use, then discarded. This minimizes the risk of contamination and transmitting diseases while saving time on sterilization. Common single-use instruments and equipment made from thermoplastics include :
- Dental mirrors
- Mouth props
- Impression trays
- Dental explorers
- Dental syringes
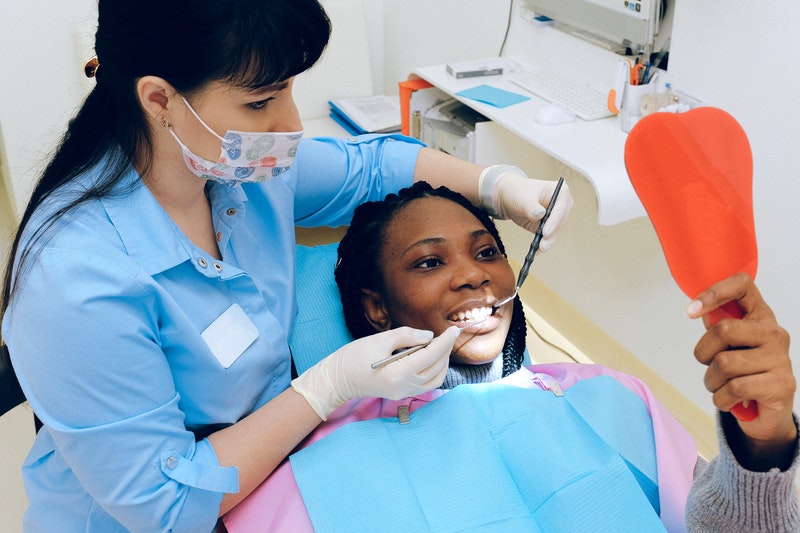
Molded Plastics Make Dental Tools More Comfortable
Thermoforming and injection molding make it affordable and easy to create single-use plastic tools, but it also makes it possible for these tools to be more comfortable, both for the dentist or hygienist and the patient. Plastics are lighter to hold for long periods of time and they can be formed and shaped to curve so they can reach difficult areas with minimal discomfort. Dental forceps and specialized syringes are particularly improved through plastic molding by curving them in a way to ensure they can access the necessary areas safely for both the dentist and patient.
Improving Sterility and Cleanliness Through Antimicrobial Plastics
We’ve talked about antimicrobial plastics before and how they are increasingly being used in medical settings. These are made with a coating that inhibits the growth of bacteria and microbes on the surface, inhibiting their spread and making it easier to keep surfaces and areas clean in between patients. Again, this helps save time while improving the cleanliness and sterility of the patient areas. From work trays to exam chairs and light cases, antimicrobial plastics are being used for a wider range of surfaces in the exam rooms.
Thermoplastics in Dental Appliances and Implants
One of the key areas where thermoplastics are improving dentistry is in dental appliances and implants. For decades, dentures and other dental appliances were made from metal, which was often painful, cutting into sensitive gum tissues and leading to a dissatisfying experience for the user. Additional issues for patients who had metal dentures or bridges was that they could damage existing teeth if it was used in a bridge or a partial, metal framing and bands were highly visible, and some users even complained of a consistent metallic taste in their mouth.
Today, acrylic resin or polyetheretherketone (PEEK) is used to make dentures, bridges, and other dental appliances. This hard, long-lasting material has the durability of metal but is significantly more comfortable to wear for long periods of time. Wearers rarely experience pain and discomfort, nor do patients need to worry about complications such as damage to existing teeth or metal sensitivity.
Contact Us to Learn More About Medical Plastic Manufacturing
At Advanced Plastiform, Inc., we are dedicated to manufacturing high-quality, durable custom plastics for all kinds of industries, including medical and healthcare. With low per-unit prices and a fast turnaround time, our injection molding company serves North Carolina, South Carolina, Pennsylvania, Maryland, Tennessee, Georgia, and Virginia.