Thermoforming Vs. Injection Molding
Exploring the nuances of plastic manufacturing methods, emphasizing quality, efficiency, and reliability of thermoforming vs injection molding techniques.
Your Source of Thermoformed and Injection Molded Plastic Parts
At Advanced Plastiform Inc., our experts in the thermoformed plastics manufacturing process pride ourselves on delivering high-quality solutions tailored to meet the diverse needs of our clients. With a commitment to innovation and excellence, we are exploring the nuances of thermoforming versus injection molding, unraveling the distinctive features, benefits, and applications of each method.
Welcome to the forefront of plastic manufacturing excellence as our thermoforming company provides insights to empower you to make informed decisions about your plastic manufacturing needs.
What is Thermoforming vs. Injection Molding for Plastics?
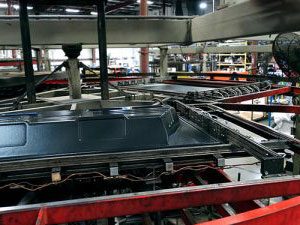
Thermoforming and injection molding are two fundamental processes in plastic manufacturing.
Thermoforming involves heating a sheet of plastic until it becomes pliable, then shaping it using a mold to create the desired form. Injection molding, on the other hand, utilizes molten plastic injected into a mold cavity under high pressure, where it cools and solidifies to produce the final product.
The Thermoforming Process
The thermoforming process requires heating plastic sheets until they become flexible and malleable, then forming them around custom-designed molding tools. This single-sided tool is generally made from aluminum, meaning it is quick to create and made from less expensive materials, reducing the initial costs of manufacturing.
At Advanced Plastiform, Inc. we use three different methods of thermoforming:
- Vacuum Forming: Vacuum forming involves pressing the heated plastic sheet to the mold and vacuuming out the air to form a tight fit against the mold. It's the quickest and most cost-effective way to form plastic parts, but because it uses the least amount of pressure, it's best for large pieces that don't require heavy detailing, sharp corners, or sharp angles.
- Pressure Forming: Plastic pressure molding works in the opposite way to vacuum forming. Once the plastic is heated and fitted around the tool, it's blasted with highly pressurized air to force the plastic against the tool, getting the sharper corners and details that vacuum forming can't.
- Twin Sheet Forming: Twin sheet forming uses two sheets of heated plastic that are pressed against one mold from opposite sides and fused where both sheets meet. Often used to make air ducts, vending machines, bed liners, and hollow or double-walled industrial products, this method requires care and precision to ensure the pieces are lined and fused with total accuracy.
The Injection Molding Process
The injection molding process involves using plastic pellets that are heated to a liquid and then injected into custom 3D injection molds using high pressure. This forces the melted plastic into every void in the double-sided mold, ensuring a highly accurate finished product. Injection molding is best used to create components with variable thickness, intricate details or ridges, and sharp corners and angles, especially for smaller plastic pieces.
Cost of Thermoforming Versus Injection Molding
When comparing the costs of thermoforming and injection molding, several factors come into play that can influence the overall expense of the two processes. Let's explore the various cost differences between injection molding and thermoforming, so that you can choose the plastic manufacturing process that best suits your project's needs.
Tooling Costs
Thermoforming typically involves lower tooling costs compared to injection molding. Since thermoforming molds are made from less expensive materials like aluminum or composite materials, they are generally more economical to produce.
Injection molding tooling molds are typically made from steel and can be significantly more expensive to operate than thermoforming tooling methods. The initial higher upfront cost of injection molding is due to the precision required of the injection molding machine performing the high-pressure process to mold parts.
Production Volume
Thermoforming is often more cost-effective for smaller production quantities. The relatively simple tooling and setup make it efficient for smaller batch sizes. In contrast, injection molding becomes more cost-effective at high volume production runs due to the faster cycle times and lower per-unit costs once the initial tooling expenses are spread out over a larger number of parts.
Material Costs
Thermoforming materials, such as sheets of plastic, tend to be less expensive compared to the thermoplastic pellets or granules used in injection molding. However, the material costs can vary depending on factors such as material type, quality, and quantity required for each process.
Labor Costs
Labor costs can vary depending on the complexity of the part and the level of automation involved in each process. Thermoforming often requires less labor-intensive setup and operation compared to injection molding, which may involve more intricate injection mold designs and machine programming.
Lead Time
Thermoforming typically has shorter lead times for tooling production compared to injection molding. This can be advantageous for projects requiring rapid prototyping or quick turnaround times, whereas injection molding may have longer lead times. The longer lead times are due to the more intricate injection mold tooling fabrication process, especially for complex part geometries.
Overall Cost Considerations
While thermoforming may offer lower upfront costs and faster tooling turnaround times, injection molding can provide economies of scale and lower per-unit costs for larger production volumes.
When determining which manufacturing process is most cost-effective for a specific application, it's best to consult with the experienced plastic molding experts from Advanced Plastiform Inc., as we can help determine the most cost-effective solution for your manufacturing needs.
Choosing Plastic Injection Molding vs Thermoforming
When deciding between thermoforming and injection molding, it's essential to understand which method aligns best with your specific needs. Neither method is inherently superior; the choice ultimately hinges on achieving the most precise final product at the lowest cost and within the shortest timeframe.
Opting for Thermoforming
Thermoforming shines under the following circumstances:
- When larger plastic pieces are required or when consolidating multiple components into a single piece is advantageous.
- For smaller orders under 3,000 pieces or for one-time production runs.
- When the final product doesn't necessitate intricate designs, varying thickness, or sharp angles and corners.
- Common applications of thermoformed plastics include vehicle dashboards, bathtubs, shipping trays, and freezer liners.
Selecting Injection Molding
Injection molding excels when the following factors come into play:
- When smaller plastic components are needed.
- For large orders or regular production cycles.
- When the component demands high levels of detail, variable thickness, and sharp or crisp angles.
- Examples of plastics manufactured through injection molding include dials and knobs in cars, packaging materials, and bottle caps.
The decision between thermoforming versus injection molding depends on factors such as the size of the order, the complexity of the design, and the desired features of the final product. By carefully evaluating these variables, you can choose the method that best meets your project requirements.
Why Choose Advanced Plastiform Inc. for Plastic Manufacturing?
At Advanced Plastiform Inc., we pride ourselves on being a trusted partner in plastic fabrication and manufacturing. Our commitment to excellence, combined with our comprehensive approach to plastic parts manufacturing, sets us apart as a leader in the field. Explore below to discover why we are your top choice for plastic manufacturing solutions in North Carolina, South Carolina, Georgia, Maryland, Pennsylvania, Tennessee, and Virginia.
Expertise Since 1988
For over three decades, Advanced Plastiform Inc. has been a leader in plastic fabrication and manufacturing. Our extensive experience and proven track record make us a trusted partner for clients across the Southeast and Mid-Atlantic regions.
Custom Solutions for Diverse Industries
Specializing in custom thermoformed and injection molded parts and components, Advanced Plastiform Inc. serves a wide range of industries, including automotive, medical, refrigeration, packaging, telecommunications, and more. We tailor our solutions to meet the unique needs of each sector, delivering high-quality products that exceed expectations.
Comprehensive Analysis for Optimal Manufacturing
At Advanced Plastiform Inc., we understand that selecting the right manufacturing method is crucial for project success. Are you unsure whether thermoforming or injection molding is best for your project? We carefully analyze various factors to determine the most cost-effective and efficient approach, ensuring the lowest cost and shortest lead time without compromising quality.
In-Depth Exploration of Manufacturing Processes
To provide our clients with a thorough understanding of plastic manufacturing, we offer an in-depth exploration of thermoforming and injection molding. By delving into the nuances of each process and the variables involved, we empower our clients to make informed decisions for their projects.
Efficient Lead Times and Cost-Effective Solutions
With Advanced Plastiform Inc., you can expect efficient lead times and cost-effective solutions.
Thermoforming typically boasts a lead time of around 14 weeks, while injection molding can take up to 20 weeks. Despite potential longer lead times, the initial tooling costs for injection molding are a one-time investment, leading to reduced per-unit costs for larger production volumes.
When you partner with Advanced Plastiform Inc., you're choosing a plastic manufacturing company dedicated to delivering exceptional results. From concept to completion, we're committed to helping you navigate the complexities of plastic production and bringing your vision to life.
Contact Advanced Plastiform, Inc. for Thermoforming and Injection Molding Solutions
Because every project is unique, determining if your custom plastics should be manufactured using thermoforming or injection molding is best done when you work with an experienced team of engineers and designers.
At Advanced Plastiform, Inc., our team is with you every step of the way, from assisting with design creation and product prototyping, to selecting the best method of manufacturing, and even providing inventory management solutions if needed.
When you are ready to get started with your custom pressure-formed or injection-molded product, contact Advanced Plastiform. Inc. for high quality, custom manufactured components for your company.
Get started by contacting us today by calling 919-404-2080 or filling out the form below to the right.