Injection Molding for South Carolina Companies
Unlocking high-quality injection molding solutions for plastic manufacturing in South Carolina.
South Carolina Injection Molding Services
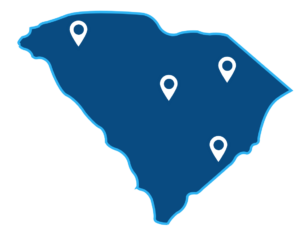
With a rich legacy of excellence in the plastics manufacturing industry, Advanced Plastiform Inc. is proud to offer state-of-the-art injection molding solutions tailored to meet the diverse needs of our clients in South Carolina.
Our injection molding experts combine decades of expertise with the latest technologies to deliver high-quality, custom injection molding services that drive efficiency and elevate product quality.
Industries Served for Injection Molding in South Carolina
At Advanced Plastiform, Inc., we design and manufacture high-quality, injection-molded plastic parts for companies across South Carolina in all types of industries, including:
Using both thermoforming and injection molding to produce plastic parts, components, and products, our customers rely on us for short lead times and competitive per-unit pricing. Additionally, our injection molded plastics are engineered with accuracy, offering consistent results, no matter how many pieces we produce.
Our Injection Molding Process
At Advanced Plastiform Inc., our injection molding process is a seamless blend of precision engineering, advanced technology, and meticulous quality control measures. From concept to completion, our plastics engineering team ensures that every step of the process is optimized to meet the highest industry standards and exceed our clients' expectations.
Design and Development
Our expert design team collaborates closely with clients to create customized molds tailored to their exact project requirements. Utilizing cutting-edge 3D modeling and CAD software, as well as prototyping techniques, we translate concepts into precise models before proceeding to the manufacturing phase.
Tooling and Mold Fabrication
Once the design is finalized, our skilled tooling engineers meticulously craft molds using state-of-the-art CNC machining equipment. With an unwavering commitment to precision, we ensure that every detail of the mold is meticulously engineered to produce flawless results. Our extensive experience enables us to fabricate molds of varying complexities, from simple prototypes to intricate multi-cavity molds.
Injection Molding
Our modern injection molding machines allow for precisely meeting injection molding process parameters, including temperature, pressure, and cycle times. Whether producing small-scale prototypes or high-volume production runs, we maintain strict adherence to quality standards to ensure consistency and accuracy in every plastic part produced.
Material Selection and Processing
Our experienced technicians carefully select the appropriate injection molding materials based on factors such as strength, durability, and environmental considerations. Through meticulous material processing and handling, we guarantee optimal performance and longevity of the finished products.
Quality Assurance
Quality is at the forefront of everything our leading plastics engineering company does. Our dedicated quality assurance team conducts rigorous inspections at every stage of the injection molding process. By adhering to stringent quality control measures, we ensure that only products of the highest caliber leave our facility.
Packaging and Delivery
Once the production process is complete, our logistics team carefully packages the finished plastic pieces to protect them during transit. Whether shipping locally in South Carolina, domestically, or internationally, we ensure timely and secure delivery to our clients' doorsteps.
Choosing Injection Molding vs Thermoforming
While thermoforming is a more popular manufacturing process option due to its lower up-front cost and faster lead times, it’s not ideal for every design. Injection molding is often chosen for small-piece mold making, items requiring variable thickness, and more complicated detailing, which often cannot be achieved through thermoforming.
Here are some key considerations when choosing injection molding vs thermoforming for your plastic manufacturing needs in South Carolina.
Precision and Detail
Injection molding excels in producing parts with intricate geometries and fine details. The process allows for tight tolerances and precise control over dimensions, making it suitable for applications requiring high accuracy and consistency.
Material Selection
With a wide range of thermoplastic and thermoset materials available, injection molding offers versatility in material selection. Engineers can choose from various resins with specific properties such as strength, flexibility, and heat resistance to meet the requirements of their application.
Volume and Efficiency
Injection molding is highly efficient for high-volume production runs. Once the molds are fabricated, the process allows for rapid and continuous production with minimal manual intervention, resulting in shorter cycle times and lower per-unit costs.
Tooling Costs
While injection molding offers cost efficiency for large production volumes, the initial tooling costs can be higher compared to thermoforming. However, these costs can be offset by economies of scale achieved through mass production.
What to Look for in an Injection Molding Company
When choosing the right injection molding company in South Carolina, it's crucial to partner with a trusted industry leader that delivers unparalleled quality, precision, and customer satisfaction.
At Advanced Plastiform Inc., we are committed to exceeding your expectations at every step of the process. Here's why we stand out as the premier choice for injection molding services in South Carolina.
Expertise and Experience
With decades of experience in the injection molding industry, our team of professionals has a reputation for excellence and innovation. We possess unparalleled expertise in designing, engineering, and manufacturing precision-molded parts and products. From concept to completion, we leverage our extensive knowledge and advanced technologies to deliver superior results that elevate your projects to new heights.
State-of-the-Art Facilities
At Advanced Plastiform Inc., we invest in the latest state-of-the-art equipment and facilities to ensure optimal performance and efficiency. Our modern manufacturing facilities are equipped with advanced injection molding machines, automated systems, and quality control measures to deliver consistent, high-quality results.
Customized Solutions
We understand that every project is unique, which is why we offer fully customized injection molding solutions tailored to your specific project and product requirements. Whether you need prototyping, low-volume production, or high-volume manufacturing, we have the expertise and capabilities to deliver results that align with your vision and objectives.
Quality Assurance
Quality is our top priority. We adhere to stringent quality control measures and industry standards to ensure that every plastic part we produce meets the highest levels of quality and reliability. From rigorous inspections to comprehensive testing protocols, we leave no stone unturned in our pursuit of excellence.
Customer Satisfaction
Advanced Plastiform Inc. prides itself on our unwavering commitment to customer satisfaction. From the initial consultation to the final delivery, we prioritize open communication, transparency, and responsiveness to ensure that your experience with us is nothing short of exceptional.
Contact Us Today for Plastic Injection Molding Services in South Carolina
If your South Carolina company needs custom plastics, Advanced Plastiform, Inc. can help. Whether your company is located in Greenville, Florence, Columbia, Charleston, or another area of South Carolina, our team of plastic engineering experts is available to handle the design and delivery of your custom plastic products, parts, and pieces.
With our dedication to customer service, we provide high-quality products on time and within your budget.
Get started today by contacting a member of our team by calling 919-404-2080 or filling out our easy-to-use contact form.
Contact the Leaders in Injection Molding in South Carolina
We're here to discuss your custom plastic manufacturing needs.
Please call us at 919-404-2080 or email us now.