Whether you need 10 parts or 10,000, custom plastic parts are affordable. In terms of…
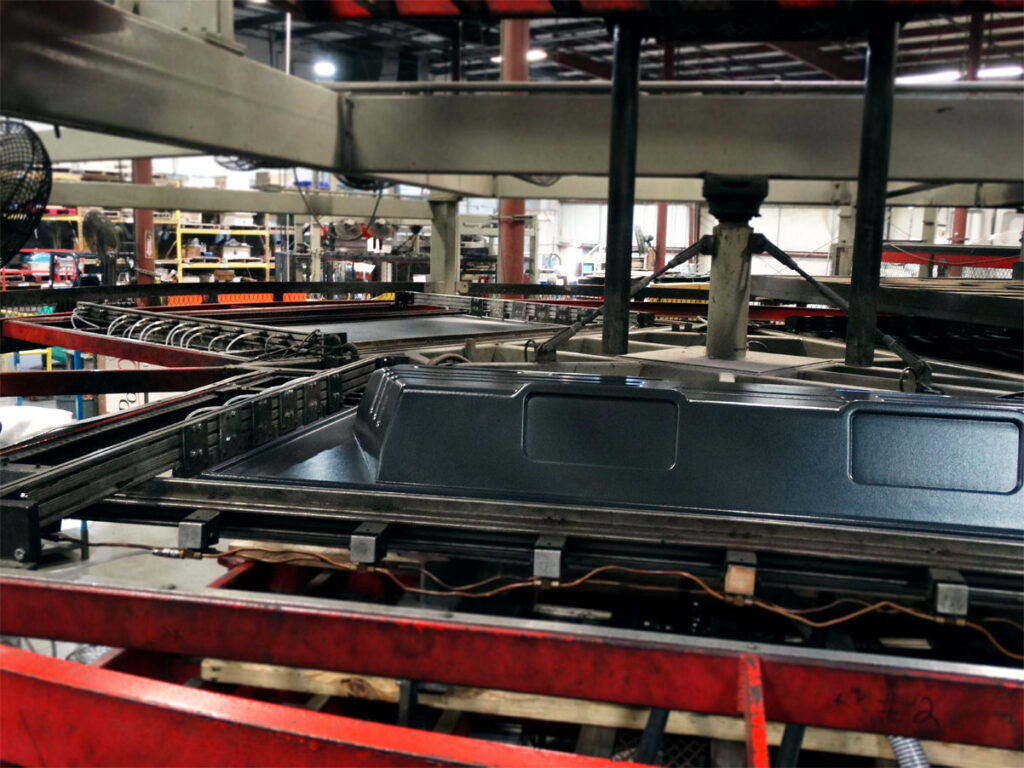
Manufacturing custom plastics isn't just about molding it into a specific shape, though that's a big part of it, of course. It's also about making sure the plastic has the properties necessary to meet the needs of the design, and often this requires additives, coatings, and other customizations to the plastic itself. For example, you want casing for wires made from polyvinyl chloride (PVC) because it's durable and resistant to impact and moisture, but PVC is a hard, brittle polymer so a casing wouldn't be able to curve with the wire. That's where adding a plasticizer to the PVC makes it softer and more flexible, making it ideal for a wire casing. Our thermoforming company is sharing a closer look at fillers and additives in plastics to help you get a look at how we achieve the necessary qualities in our customers' custom plastics.
What Are Plastic Additives and Fillers?
Additives and fillers are organic or inorganic compounds that are introduced into a plastic in order to change the properties of the plastic. While most plastics in their original form are impact resistant and long-lasting, they are often brittle, hard, combustible, or too heavy for the intended use. Adding additives or fillers can transform the plastic so it meets the intended use without sacrificing the qualities that made it attractive in the first place. The PVC wire casing example above is just one example, but nearly every plastic has some type of additive included to optimize it for the intended use.
Plasticizers Used for Flexibility
The most common additive in plastic are plasticizers. These are typically liquid, non-volatile organic substances that improve flexibility, particularly when thermoforming, shaping, and molding. Most often used in PVC, plasticized PVC is in automotive thermoforming, flooring, roofing, and cables. You'll also find plasticizers used in acrylics, PET, and polyolefin.
Most plasticizers are esters that are created when acids react with alcohols, and the amount added affects the finished product. For example, vinyl gloves consist of around 50% plasticizers so they are pliable and comfortable to wear.
Fillers Reduce Cost and Weight
Often, minerals such as calcium carbonate, silica, clay, kaolin and carbon are added as fillers to polymers. While most people think these are simply used to add bulk and lower cost, many of these mineral fillers make them easier to mold and shape while ensuring the stability of the compounds. For plastics that require heat-resistance, mineral fillers can increase heat-deflection and reduce thermal expansion.
Carbon Fillers in Plastic
Carbon fibers are frequently added to polymers because they add several benefits, including increasing the tensile strength without adding weight, improving heat deflection, and improving electrical conductivity.
Polymer Stabilizers Increase Lifespan
While we've discussed antioxidants in plastics at length, we also wanted to touch upon them here, too. Polymer stabilizers are chemical additives that inhibit or slow down degradation caused by oxidation, UV exposure, and heat degradation as well as minimizing the reactions with catalysts that could break down the plastic at the chemical structural level. In addition to antioxidants that block the autoxidation that takes place when a polymer reacts with oxygen in the atmosphere, additional stabilizers include:
- UV absorbers
- "Quenchers" that absorb energy created when light reacts within the polymer.
- Acid scavengers
- Metal deactivators
- Heat stabilizers
Flame Retardants
Flame retardants are a type of stabilizer, but they stand out because they improve fire resistance and minimize the risk of combustion. Most thermoplastics are flammable and, when introduced to a high temperature, are designed to bend and melt. Adding flame retardants delay ignition and burning, minimize smoke, and reduce the spread of flames, which keeps people safe and minimizes property damage, but they also offer long-term benefits by reducing free radicals. Aluminum hydroxide, phosphorus compounds, and brominated compounds are the most common types of flame retardants.
Call Us for a Quote on Custom Plastics Today
At Advanced Plastiform, Inc., we offer comprehensive plastic manufacturing services, all the way from design to drop shipping, for a wide variety of industries. With low per unit pricing and fast lead times, we make durable, high-quality custom plastics affordable and accessible to customers across the Mid Atlantic and Southeast, including North Carolina, South Carolina, Pennsylvania, Maryland, Tennessee, Georgia, and Virginia.
Contact Advanced Plastiform, Inc.
Let Us Know How We Can Help!