Learn more about knit lines in injection molding - what they are and how to…
Plastics manufactured by injection molding are meant to be durable and reliable, able to hold up to heavy use, high temperatures, or adverse conditions. One of the things that can compromise an injection molded part is a weld line, also called a knit line. Our injection molding company is explaining what these imperfections are, why they can compromise a part or product, and how we avoid them.
What Is a Weld Line?
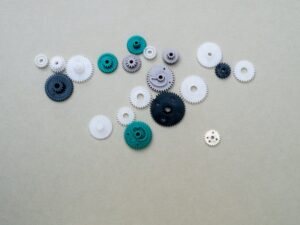
In injection molding, a thermoplastic material is melted to a liquid state and injected into a custom, double-sided mold. When the plastic cools, it takes the shape of the mold and is then ejected and finished. A weld line, or knit line, occurs when two flows of melted plastic meet and "knit" together.
For molds with obstructions, such as angles, corners, or edges, the melted plastic may hit the obstruction and split into two separate flows. When they rejoin, if the two flows do not mix back together, or meld, into one flow, a visible line caused by an air pocket or an additive such as lubrication will form.
Why Are Weld Lines Serious?
Weld lines are more than just a cosmetic flaw in the plastic (often they're barely visible at all). When there is a separation between the plastic, whether that void is filled with air or a plastic additive, this creates a weak point because the polymers don't meet at all to bridge the gap.
How to Avoid Weld Lines During Injection Molding
Once a weld line is present in plastic, it can't be removed, so it's important to prevent them before they occur. Below is a list of suggestions for avoiding weld lines during the injection molding process:
Adequate Pressure
In order for two flows of plastic to meld back together and avoid the air pocket, the injectors must have adequate pressure for the plastic to move with the proper speed and force. This will also ensure that both flows of plastic are moving at the same rate, improving its ability to meld back together.
Temperature
When the temperature of the plastic isn't hot enough, it may solidify too quickly. Even if it's still flowing, if it's too cool, it won't meld with the other plastic flow. Having the plastic at the optimal temperature during injecting and forming is key to avoiding weld lines.
Mold Design
A poorly designed mold may have too many obstructions, improperly placed gates, or walls that are too thick in places. All of these can slow down the plastic flow, causing it to cool too quickly and lose pressure, both of which are the most likely reasons for weld lines in injection molding.
Plastic Purity
When a poor-quality plastic that has impurities in it is used for injection molding, it is less likely to flow smoothly through the mold.
Receive a Free Quote for Injection Molded Plastics
At Advanced Plastiform, Inc., we have over three decades of experience and knowledge in injection molding and thermoforming. Our custom plastics are designed to be durable, tough, and resilient, and we are proud to offer low per-unit prices with fast lead times. We serve the entire Southeast and Mid-Atlantic, including North Carolina, South Carolina, Pennsylvania, Maryland, Tennessee, Georgia, and Virginia. To learn more about our services or get a free quote, reach out to us today by giving us a call 919-404-2080 or filling out the easy-to-use form below.