Twin sheet thermoforming can be complicated, but we're sharing troubleshooting tips to get the best…
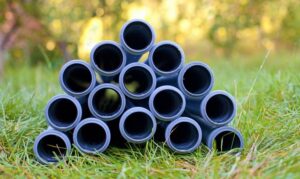
Hollow plastic components and products are necessary for everything from air ducts and pipes to water bottles, and if you need hollow plastics, you want a fast, cost-effective method of manufacturing them that won’t sacrifice quality or structural integrity. The two most common methods of forming and shaping these products are blow molding and twin sheet thermoforming. Our plastics manufacturing company is providing a closer look at each process and why twin sheet thermoforming may be the right choice for your company.
Understanding Twin-Sheet Thermoforming
Twin sheet thermoforming is a process in which two sheets of plastic are heated until pliable then fitted around two custom molds at the same time. After the sheets are shaped using pressure or vacuum forming, they are then fused together. Using this method, we can construct double-walled and hollow pieces efficiently and precisely, while still providing the faster lead times and low costs that are a benefit of heavy gauge thermoforming.
Why Choose Twin Sheet Thermoforming?
This method is most often used when heavy-duty, durable parts or components are needed. This manufacturing process can be completed with almost any type of thermoplastic, including ABS, PVC, and Thermoplastic Olefin, which allows for more structural stability, impact resistance, and durablity while still creating a light-weight product.
Additional benefits of twin sheet thermoforming include:
- Structural reinforcements and internal components can be used or added;
- Molded-in attachments can be included in the design;
- Coatings, texture, and other customizations and finishes can be applied;
- Inexpensive tooling that can be fabricated in just a few weeks;
Twin-sheet thermoforming is ideal for small to mid-size production runs and creating industrial strength hollow and double-walled pieces, that include:
- Bed liners
- Air ducts
- Industrial pipes
- Drain pipe extenders
- Vending machines
Understanding the Extrusion Blow Molding Method
Extrusion blow molding is more similar to injection molding, in which a thermoplastic is melted to a liquid. At that point, it’s then shaped into a hollow tube, called a parison, inside a custom mold. Once the parison is in place and still soft, pressurized air is blown into it, causing it to expand from the inside (like blowing up a balloon) and filling the shape, creating the finished product.
Why Choose Blow Molding?
Blow molding is most often used with lightweight plastics, like polyethylene terephthalate (PET), and with products that require large or ongoing production runs. While the tooling fabrication is often more expensive and requires a longer lead time than twin sheet forming, once it’s available, it can be used permanently. You’ll often see blow molding used for smaller products like water bottles, where a thin, hollow item is needed.
Additional benefits of blow molding include:
- Manufacturing and production is fast once tooling is in place;
- Very lightweight end results;
- Exterior detailing can be as intricate as needed, even on small items;
While blow molding isn’t right for heavy plastics, items that need double walls, panels, or additional components, it does have a place in plastics manufacturing.
Contact Us for High Quality Twin Sheet Thermoforming
If you need accurate, high-quality custom plastics created through injection molding or thermoforming, we can help. We work with all types of industries in the Southeast and Mid-Atlantic, including North Carolina, Pennsylvania, Maryland, Tennessee, Georgia, and Virginia. To learn more, reach out to our team today.
Contact Advanced Plastiform, Inc.
Let Us Know How We Can Help!