Learn how thermoplastics offer the durability and versatility needed to support our telecommunication infrastructure.
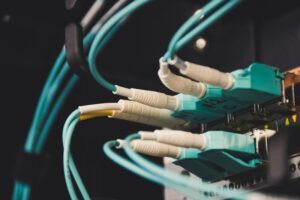
When most people think of telecommunications, they think of long lines of code or bundles of wires. While all that is definitely important, we know it’s the hardware that makes communication possible, and much of that hardware is made from thermoplastic materials. In order to ensure durability and protect delicate electronics to keep data and communication flowing smoothly, the right materials have to be chosen for the task. Our thermoforming and injection molding company is sharing a closer look at the thermoplastics used in telecommunications and why they’re chosen for the job.
Acrylonitrile Butadiene Styrene
ABS or, Acrylonitrile Butadiene Styrene, is one of the key players in manufacturing telecommunications hardware and it’s often used to make keyboards and keys, computer and laptop casing, and the exteriors for routers. What makes it so appealing? The main benefit is that it’s very strong and rigid, so it has a very high impact resistance and long-lasting durability, plus it’s heat resistant, so if equipment runs hot, the housing and casing won’t be damaged. On top of this, ABS is inexpensive and easy to manufacture so whether it’s thermoforming a router casing or injection molding keyboard keys, it’s a quick project with low per-unit costs.
Polyvinyl Chloride
PVC, also known as Polyvinyl Chloride, in its pure state is incredibly hard and rigid, making it a great material for plumbing pipes. However, it’s also one of the most versatile polymers because with the addition of plasticizers, it can be softened and shaped without losing its durability. Because of this, and several other features, PVC is the ideal material to insulate and protect cables, cords, and wires.
Not only is PVC durable, flexible, and easy to produce, but just as important, it doesn’t conduct electricity. From the internal wiring of a laptop to the casing on a cat 5 ethernet cable, manufacturers rely on PVC to keep their wiring safe.
High Molecular Weight Polyethlyene
In the 1850s, submarine cables were laid in order to send telegraph communications overseas. For the next over 150 years, subsequent generations of cables were laid on the bottom of the ocean for telephone traffic and data communications. Today, fiber optic cables are used instead, lying on the ocean floor to carry telephone, internet, and digital data from one continent to another.
Polyethylene (PE) is one of the primary components of the submarine cables because it is resistant to abrasion, moisture, and impact, plus it’s non-conductive. Near the coasts, where the water is more shallow and there’s more commercial traffic, cables are covered in a steel shell and buried into the bottom. The further from the shore as the water gets deeper, the outer surface of the cable is a simple polyethylene sheath that holds up to constant salt water exposure and freezing temperatures as it rests hundreds of feet below the surface.
Call Us for Telecommunications Injection Molding and More
As the telecommunications industry continues to grow and expand, we’re growing with it to design and manufacture custom plastics that offer the durability our customers need along with low per unit pricing and fast turnaround times. We’re dedicated to providing high quality plastics that keep communication moving forward.
We work with all types of industries in the Southeast and Mid-Atlantic, including North Carolina, Pennsylvania, Maryland, Tennessee, Georgia, and Virginia. To learn more, reach out to our team today.
Contact Advanced Plastiform, Inc.
Let Us Know How We Can Help!
"*" indicates required fields